The biotechnology industry is expanding into the fashion industry, with investors backing leather substitutes made from mushrooms, animal cells or recombinant collagen produced in yeast. On January 13, MycoWorks announced a $125 million round of funding that will finance a full-scale production plant in South Carolina to make a leather alternative from Ganoderma lucidum mycelium. This follows last year’s $7 million toward a funding round by VitroLabs, which grows hide from animal cell cultures.
“We’ve definitely seen an influx in the last couple of years of biotech companies that are founded in the fashion and materials space,” says Fiona Mischel, director of international outreach at Built with Biology (formerly SynBioBeta) in London. “Their goal is to remake the fashion industry with sustainable materials,” she says. Cow hide and current fake, fossil fuels-based alternatives are toxic and wasteful, these companies say. Leather production requires raising and slaughtering animals, which has a high environmental footprint, and the tanning process often uses toxic chemicals like chromium. Biotech leather does not need to be finished in the same way, so fewer chemicals are used. And current faux leather, or ‘pleather’, is not only made with plastic polymers from non-renewable fossil fuels, but it is also not readily biodegradable.
So biotech entrepreneurs are jumping into the leather substitute business, wielding a range of creative biotech approaches (See table). One technique grows mushrooms on a substrate (for example, agricultural waste, corn cobs, hemp hurds, paper pulp waste, rice hulls or sawdust) under tightly controlled environmental conditions to mimic leather Another cultures mammalian cells to form leather-like sheets. Still another genetically engineers microbes to produce collagens, which are then turned into textile fibers. Many of the bio-based materials have the same properties and aesthetics as leather, allowing designers to substitute them for animal leather.
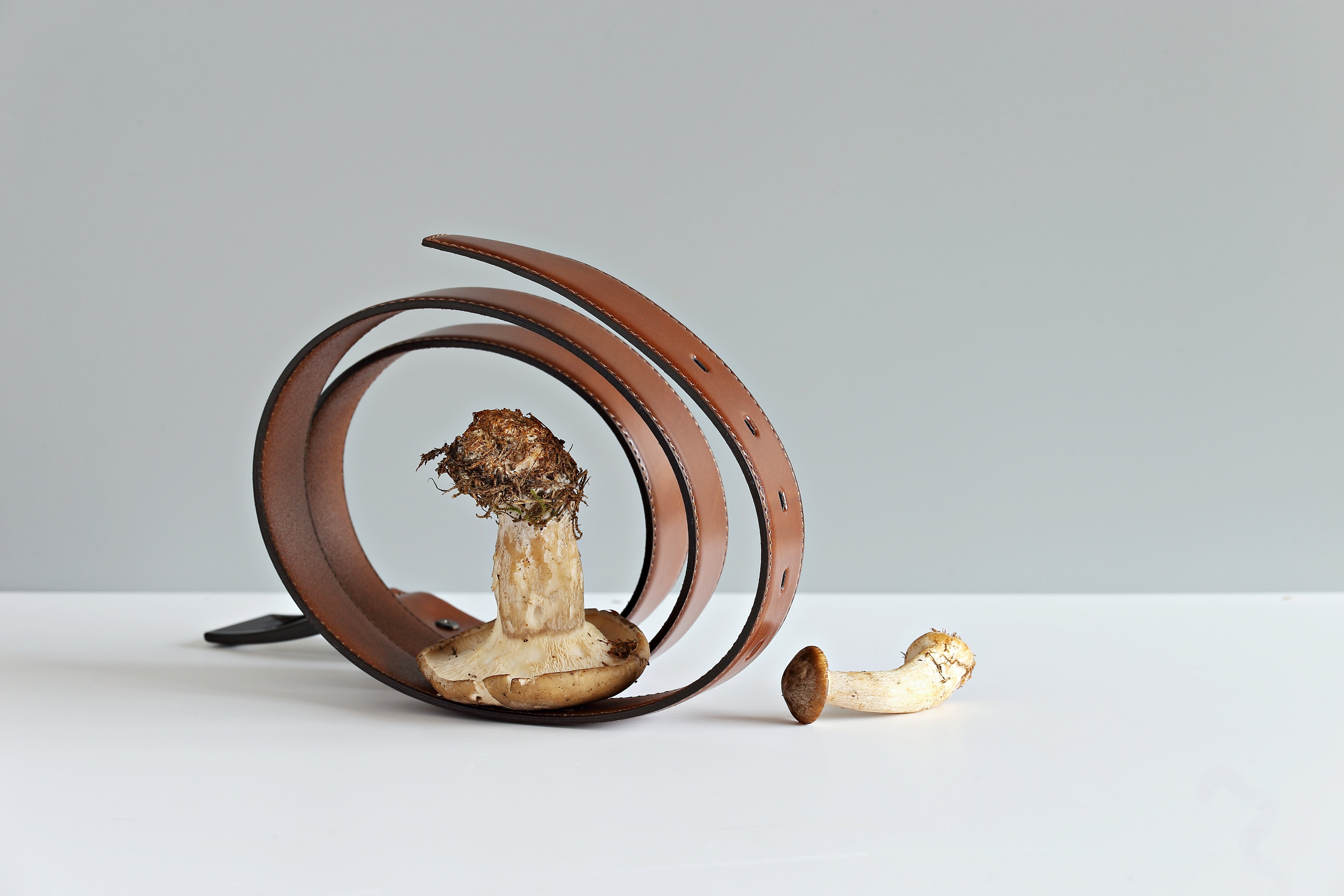
VitroLabs, for instance, grows its product from cells. In their process, scientists coax undisclosed immortalized cell lines to grow in a nutrient-rich environment. With the help of scaffolds, the cells form tissue with the complexity of real animal hide without the need to slaughter animals. The process is similar to that used by the cultured meat industry, in which cell lines taken from animal muscle are grown in bioreactors and combined with biocompatible scaffolds for cell growth and maturation to produce an edible meat substitute. VitroLabs will benefit from advancements and investment in the food side of this industry—an effort that is lowering costs of the growth medium and driving innovation in scaffolds.
Rather than using complex cell culture procedures, other companies are isolating proteins that can be linked to form biomaterials with properties similar to leather. Hide Biotech in London makes a leather alternative out of isolated collagen proteins. The proteins come from scales, skin and other fish waste. The company’s undisclosed enzymatic and chemical process helps build and strengthen a protein network into a material that is translucent. Dyes and fat liquors can be added to the material as it is formed, eliminating the need for a separate dyeing or tanning process, says Yudi Ding, co-founder of the company.
Other companies are taking advantage of biological processes to create leather substitutes. MycoWorks, for example, grows the fungus from the species G. lucidum in trays of sawdust the size of half of a cow hide. Researchers coax the fungus to grow and branch into thread-like filamentous structures called hyphae (collectively termed mycelium) using proprietary tricks that involve controlling temperature, humidity, carbon dioxide levels and other aspects of the fungus’s environment. The fungus colonizes the trays, resulting in a material that, through an undisclosed proprietary procedure, looks and feels like leather, according to the company. MycoWorks announced last year that it had partnered with Hermès, a top-end leather goods manufacturer, to supply the material for a luxury handbag called Victoria, which is expected to reach shelves this year.
In Arequipa, Peru, Le Qara ferments a consortium of native, undisclosed microorganisms to produce a biopolymer that it then formulates via an undisclosed process into a textile with properties similar to leather. The biomaterial can support the high temperatures and pressures that machines use to finish animal leather, says Jacqueline Cruz, co-founder of Le Qara.
All these technologies are creative, but every company working in this space faces the same central challenge: matching the quality and texture of real animal leather. The fashion industry’s expectations are particularly high. “Nobody is willing to sacrifice quality and performance for sustainability,” says Matt Scullin, CEO of MycoWorks. “Animal leather is the original performance material. It is something that has a very rare combination of hand feel, warmth, breathability, aesthetic and durability. And when you combine all of these properties, you create this emotional response that leather gives us. It’s very powerful and it’s very valuable. So the bar is very high,” he says.
Many in the biotech sector say their textiles meet, or come close to, that high bar for leather. And they aim for biotech leather to beat the performance of plant-based leather alternatives, such as those made from cactus, pineapple, seaweed and apple peels. MycoWorks has sent its material to the independent testing firm Vartest. MycoWorks says that its material meets the performance standards of cowhide in durability, color fastness and tensile strength.
In addition to the realistic feel and quality of the material, biotech leather companies also face the challenge of producing their textiles at scale, at a price that competes with animal leather. That’s not an easy matter for companies tinkering with the finicky biology of living things or cultured cells. Historically, biology in competition with fossil fuels has proved too challenging. Many companies in the mid-2000s tried to produce biofuels from algae, but ran into a wall when they attempted scale up at a price point that could compete with crude oil. One of the leaders in that field, Amyris, ended up pivoting to genetically engineered yeast that produce high-value specialty molecules for fragrances, skincare, food and beverages, and pharmaceuticals. These kinds of products command price points that match the production volume that the biology allows.
Some alternative leather companies have already pivoted. Modern Meadow formed in 2012 to grow animal hide in the lab by culturing mammalian cells, but changed course when it determined that making a high-quality material at scale would take too much time and money, says Anna Bakst, the company’s CEO, who first joined the company’s board in 2017 after it shifted gears.
The company now sources proteins from plants. "It's a more sustainable approach to doing business because we're leveraging existing know-how and infrastructures," she says. The platform also enables the company to more quickly evolve to meet the desires of clothing brands, Bakst says. "Fashion moves quickly—the industry has a faster cycle than [biotech] R&D," she says.
Modern Meadow plans to apply its plant-based polymer blend to a range of textiles, including leather-like ones. Last October, the company announced a joint collaboration with Italian textile maker Limonta following a $130 million round of venture financing.
Company (location) | Products | Technology | News, partnerships, and investment |
---|---|---|---|
VitroLabs (Milpitas, California, USA) | Cellular leather | Cells derived from animal biopsies grow in a nutrient-rich environment with the help of bio-based scaffolds, forming into tissue with the complexity of an animal hide. | September 2021: $7 million funding round |
Le Qara (Arequipa, Peru) | Biopolymer-based textile with properties similar to animal leather | Undisclosed microorganisms fed with plant residues are fermented to produce a biopolymer. The biomaterial can support the high temperatures and pressures of machines used to finish animal leather. | Finishing the building of a pilot plant |
Bolt Threads (Emeryville, California, USA) | Mycelium-based leather alternative | Mycelial cells are fed sawdust and organic material in a tray while controlling the humidity, temperature and other variables. | Has partnered with Adidas, Kering, Lululemon, Stella McCartney, Mercedes Benz and Ganni |
MycoWorks (Emeryville, California, USA) | Mycelium-based leather alternative | Fungal species Ganoderma lucidum (reishi) are grown as mycelium by controlling temperature, humidity, carbon dioxide levels and other aspects of the fungus’s environment. | $125 million financing round on January 13; will build commercial production plant within a year |
Hide Biotech (London, UK) | Proteins extracted from fish waste for leather alternative | Isolated proteins from scales, bones and other fish waste are engineered with enzymes, chemicals and dyes to create a leather alternative. | August 2021: $1.35 million investment |
Modern Meadow (Nutley, New Jersey, USA) | Plant-based protein biopolymer for a range of textiles. |
The company combines plant-based proteins with a bio-based polyurethane to create a polymer blend they call Bio-Alloy. |
Oct. 2021: formed BioFabbrica a joint venture with Italian textile and materials company Limonta. April 2021: announced $130 million funding round |
Newlight Technologies (Huntington Beach, California, USA) | Polyhydroxybutyrate (PHB)-based leather alternative from air and greenhouse gases | Undisclosed native microorganisms convert oxygen from air and carbon from methane or carbon dioxide to PHB, which is used to form a leather-like material. Consumers can track the carbon impact of each product using IBM-powered blockchain. Sold under brand Covalent Fashion. | Partnership with Nike |
Bucha Bio (New York) | Nanocellulose-based biocomposite for leather alternative and other materials | Bacterial microorganisms such as Gluconacetobacter xylinus are fermented to produce nanocellulose, which is formulated with plant-based components into various biocomposite materials. | Accepted into IndieBio startup accelerator in 2021; Raised $550,000 pre-seed funding round in November 2021 |
Ecovative (Green Island, New York, USA) | Fungus-based leather alternative | Undisclosed fungus strains are grown as mycelium on long beds by controlling the atmosphere and other aspects of the fungus’s environment. The mycelial cells are fed agricultural and forestry by-products. | Formed a fashion cooperative with Danish affordable fashion retailer Bestseller and Tommy Hilfiger parent company PVH to reach scale for mass market |
Source: Built with Biology (formerly SynBioBeta)
Beyond the challenges of scaling and performance, leather-substitute companies will also have to contend with the animal leather industry, which has fiercely fought against the use of the term “leather” for anything that doesn’t come from an animal. “We can say it’s ‘inspired by leather,’” says Ding at Hide Biotech, “but we avoid calling the material ‘leather’ because I think it will trigger the leather industry.” Indeed, several European countries have regulated the use of words for hide or leather for non-animal textiles, in response to the animal industry’s demands.
So the difficulties facing biotech leather are substantial, but the sustainability argument is on their side. Raising cows and other animals for their meat and hides contributes to deforestation when forest land is converted to pasture. The process for cleaning and tanning hides produces waste and effluent containing polluting chemicals. Plus, a hide is often sourced, tanned and finished at different locations around the world, sending it traveling tens of thousands of miles before it reaches the consumer.
International climate change accords and new policies may push fashion brands toward more sustainable materials. For example, the New York state in January introduced legislation that would require brands to map their supply chains and publish an environmental sustainability impact report.
Beyond the sustainability argument, fashion designers may come to find that that they simply need alternatives. “The leather supply chain was reaching its limits—and this predates the pandemic,” says Scullin of MycoWorks. The availability of the material varies from season to season, and as it’s a co-product of the beef industry. Purchasers of leather don’t have control over what they’re going to get, he says. “So the industry,” he notes, “is looking at their supply chains and trying to figure out where they’re going to get high-quality materials for the next 20 or 30 years.”
Biotech offers not only an alternative that mimics leather, but an opportunity to do more with a textile. “It’s one thing to have a material, but it’s another thing to take that and continue to enrich that material and evolve that material so that you can serve the different needs of the brands,” says Bakst of Modern Meadow. Adds Scullin: “We’re really excited about the ability to further tune the biology to open up new functionalities that leather does not have.”
This article is reproduced with permission and was first published on March 16 2022.