There’s a soap dish for sale at a beauty products shop in São Paulo, Brazil. An off-white disc with a smooth, rounded shape like a river stone, it is just one of millions of plastic soap dishes on offer in shops around the world. But, although most plastics are made from petroleum, some of the plastic in this dish started out as methane generated by a water-treatment facility in California.
Inside a 10-metre-tall bioreactor at the facility, ancient bacteria known as methanotrophs transformed the methane into a molecule called poly(3-hydroxybutyrate), or P3HB. The bacteria use P3HB as a kind of internal battery for energy storage. But a biotechnology company called Mango Materials in Redwood City, California, uses P3HB as a raw material, harvesting granules of it from the bacteria and manufacturing them into lentil-sized pellets called nurdles. These nurdles, the common currency of the plastics industry, then became the soap dish.
Mango Materials is part of a growing effort among scientists, non-governmental organizations and companies large and small to make plastics more sustainable. “We have a long, long way to go,” says Molly Morse, a biopolymers engineer and chief executive of Mango Materials. The company produces less than 45 tonnes of P3HB annually, a mere nurdle-sized amount of the estimated 400 million tonnes of plastic produced every year. Plastic can be found in food packaging, building materials, electronics, clothing and a host of other aspects of modern life.
The plastics industry depends on non-renewable resources. More than 90% of global plastic production consists of primary plastics—which are newly manufactured, rather than recycled—made from petroleum products. This reliance requires a huge amount of energy and produces greenhouse-gas emissions. By 2050, emissions from plastic production could amount to 15% of the estimated carbon budget needed to keep global warming below 1.5 °C (ref. 1).
Plastics also create a massive waste management issue. “The sheer volume of waste that’s created is unlike any other supply chain,” says Katherine Locock, a polymer chemist at the Commonwealth Scientific and Industrial Research Organisation (CSIRO) in Melbourne, Australia.
Roughly 70% of the plastics that have ever been produced have already been discarded2. Single-use plastic, especially packaging, makes up around 40% of plastic production in Europe3. Yet the most widely used plastics persist in landfill sites or the environment for decades or even centuries after being thrown away.
In theory, many commonly used plastics can be recycled. But only about one-tenth of the plastics that have ever been produced have been recycled once, and only about 1% have been recycled twice4. “It is cheaper to just make a new plastic product than to collect it and recycle it or reuse it,” says Kristian Syberg, who studies plastic pollution at Roskilde University in Denmark. “That’s a systemic problem.”
Changing that picture will require action on multiple fronts: scaling up established recycling technologies, rolling them out across the world, developing technologies to deal with hard-to-recycle plastics, leveraging insights from nature to aid both production and disposal of plastics, and reining in the production of single-use plastics. But the results could have benefits for the circular economy more broadly. “There’s a lot we can learn from what’s happening in the plastic space, which is incredibly active, to apply to other sectors,” says Sarah King, a circular economy researcher at Swinburne University of Technology in Melbourne, Australia.
A better sort
Studies show that to make plastics more sustainable, recycling needs to be massively scaled up worldwide. Most of the plastic recycling that occurs today is a type known as mechanical recycling. Plastic waste is collected, cleaned, sorted, shredded and then melted down and formed into pellets to be sold to producers of recycled plastic products.
The process sounds straightforward but it is far from simple in practice. “With plastics, the problem is there’s so many different types,” says Ed Cook, who studies waste plastics as part of the circular economy at the University of Leeds, UK. Different types of plastic don’t mix well when they are melted down and small amounts of the wrong type can degrade the quality of a whole batch, so plastic has to be carefully sorted first.
In high-income countries, this sorting usually happens with the help of high-tech machines at large-scale recycling facilities. These facilities typically target the most commonly used plastic types, especially polyethylene terephthalate (PET, used to make fizzy drink and water bottles), high-density polyethylene (HDPE, found in milk and shampoo bottles), and sometimes low-density polyethylene (LDPE, used for plastic carrier bags) and polypropylene (bottle caps and crisp packets).
Even with diligent sorting, recycled plastic is almost always of lower quality than primary plastic. More than 10,000 different additives can be used to give plastics different colours and technical properties. Plastics of the same type often contain different combinations of additives, resulting in recycled material with unpredictable and often suboptimal additive combinations. Plus, the long polymer chains that make up these materials become slightly shorter each time they are melted down.
All these factors mean that plastic recycling usually amounts to downcycling—creating products with less stringent technical or aesthetic qualities. For example, a food-grade plastic beverage bottle becomes a fleece garment, or components for a park bench.
Because manufacturers can’t make many products with recycled plastic, the market for it is limited, says Magdalena Klotz, a graduate student of ecological systems design at the Swiss Federal Institute of Technology (ETH) in Zurich, Switzerland. Klotz and her collaborators have shown that even if 80% of plastic in Switzerland was collected for recycling, at most only about 20% of it would wind up in recycled plastic products5. “It’s not sufficient if we only collect more,” she says. Without other changes to the plastic system, “we get secondary material which cannot be utilized”.
To streamline mechanical recycling and improve the quality of secondary plastics, some researchers are working to develop chemicals called compatibilizers, which help different types of plastic to mix together evenly when they are melted down. “This is an old field, but the idea of applying it to recycling has gained a lot of traction more recently,” says Megan Robertson, a chemical engineer at the University of Houston in Texas. Several compatibilizers that can aid mixing of specific types of plastic are now commercially available, and Robertson is working to develop a more flexible compatibilizer that could be applied to diverse mixes of polymers.
Other efforts aim to improve sorting to ensure a purer, more uniform stream of plastic entering the recycling process. The HolyGrail 2.0 project—a collaboration between more than 160 companies and organizations involved in plastic packaging, facilitated by the European Brands Association and funded in large part by the Alliance to End Plastic Waste—is piloting the use of digital watermarks in Europe. These are codes embedded in plastic packaging that can be read by specialized cameras in recycling facilities and contain information about the attributes of a piece of plastic waste, such as the additives it contains. Another approach is known as aligned design, which calls on plastics manufacturers to coordinate to make products with fewer types of plastic and use the same set of additives. Then recycling facilities would receive a larger volume of similar plastics, in turn yielding higher quality recycled plastics. “An easy win would be to simplify things a little bit more,” Cook says.
Some companies are starting to take these ideas on board. In August, the Coca-Cola Company based in Atlanta, Georgia, began packaging Sprite, its lemon-lime carbonated drink, in clear plastic bottles in North America, rather than the iconic green bottles it has used for 60 years. The goal, the company says, is to aid the recycling of its bottles back into bottles, rather than into other products that are harder to recycle. That, in turn, will help Coca-Cola to meet its own pledge to increase the amount of recycled content in its packaging. The move highlights what researchers say is key to increasing recycling rates: boosting market demand for secondary plastics. “We really could solve this waste problem of plastics if the people making plastics need this waste as a feedstock,” says André Bardow, a chemical engineer at ETH Zurich. “And that makes me hopeful.”
Global improvisation
Plastic is cheap to produce, an accessible and practical material for people living in informal and remote settlements with little access to refrigeration and sanitation. Additionally, its light weight makes it less energy intensive to transport than other food and beverage packaging materials. As a result, these products are found everywhere in the world, even in the remotest places, says Costas Velis, a sustainability scientist at the University of Leeds.
And there’s the catch: because waste plastic has so little value, there’s no economic incentive to collect it from those isolated locations. Indeed, plastic waste is pervasive through many low- and middle-income countries, where formal recycling programmes are rare. In fact, an estimated two billion people worldwide lack access to regular waste-management services6. Most of the estimated 13 million tonnes of plastic that enters the oceans annually comes from areas with inadequate waste management.
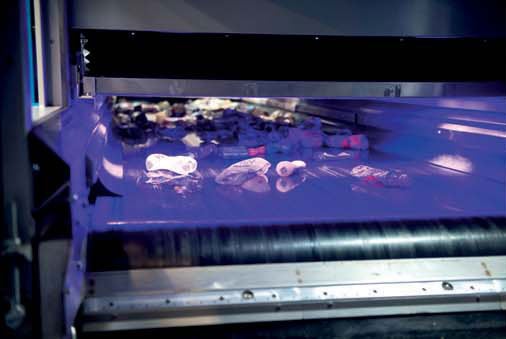
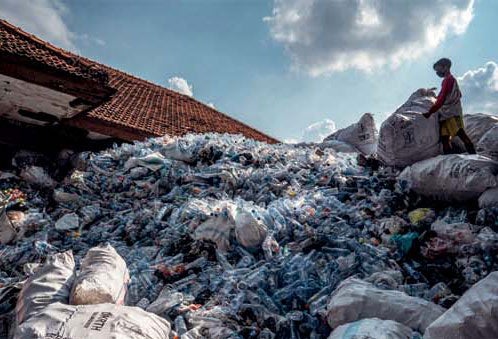
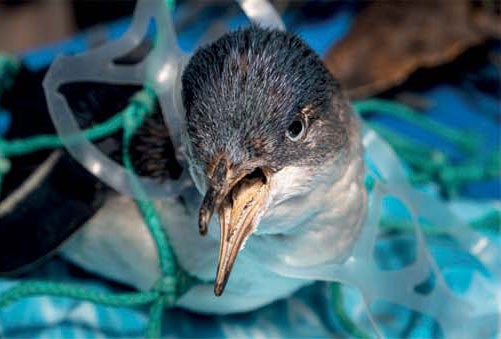
Nevertheless, a surprising amount of plastic recycling happens in low- and middle-income countries. In these places, recycling tends to be part of the informal economy. Waste pickers sift through landfill sites and bins and collect plastic from the environment. Research by a team including Velis and Cook has shown that these people’s efforts add up: “The waste pickers are behind more plastics recycling globally than the formal industry,” Velis says.
These informal workers are often entrepreneurial and adaptable. In Ghana, waste collectors have begun going door-to-door purchasing some of the most desirable plastics such as HDPE for recycling, says Kwaku Oduro-Appiah, a waste-management scientist at the University of Cape Coast in Ghana. In turn, Oduro-Appiah says, “some householders are now seeing some value and would not want to add [plastic] directly to the waste”. Other waste collectors go to events such as weddings and collect the disposable plastics used there, realizing that the cleaner plastic will fetch a higher price than items that have been picked out of a landfill, he says.
However, waste pickers and collectors in Ghana and other low- and middle-income countries tend to be living in poverty, often come from marginalized communities and their waste-collection activities are sometimes criminalized. Their work can be hazardous, especially in landfill sites, and “they don’t get even value for money because they don’t have the power to bargain”, Oduro-Appiah says. But that’s beginning to change. Recognition of the waste pickers’ contributions and concern for their working conditions is prompting efforts to include them in waste-management planning, such as in Ghana’s National Action Roadmap for plastic waste that launched in 2021.
Some of the plastic collected by waste pickers ends up at recycling plants in larger countries such as Brazil and Indonesia, which have local plastics industries. Some is shipped abroad for recycling. Some is recycled locally by small-scale businesses, with workers turning to YouTube videos to learn and share skills. “These are very small-scale operations without any environmental and public-health protection,” Velis says. Still, “there’s a lot of improvisation across the global south”, he adds.
Advanced breakdown
Although efforts continue to boost established recycling approaches around the world, the past decade has also seen increasing research attention turn to advanced recycling technologies, sometimes called chemical recycling. These methods have not yet been employed widely on a commercial scale, but they could eventually allow recycling of plastic types and products that can’t be mechanically recycled.
One such method is pyrolysis, a procedure in which plastics are heated to high temperatures in the absence of oxygen. This causes the polymer chains to break down into smaller components. Pyrolysis can be used for mixed plastic waste—potentially enabling the recycling of various products composed of multiple layers of different plastics.
So far, most research on pyrolysis has focused on turning plastic into fuel—an energy-intensive process that results in the carbon contained in the plastic being emitted into the atmosphere. But in theory, the smaller molecules that pyrolysis yields could be reassembled back into plastics.
Another advanced recycling approach is to break down plastic molecules into their individual subunits. These could then be reassembled into polymers, circumventing the shortening chains and degradation of quality that happens with mechanical recycling. This could aid the recycling of thermosets—a class of polymers that cannot be melted down, and therefore cannot be mechanically recycled. These polymers are used to produce materials such as bakelite, melamine and the epoxy resins used in wind-turbine blades.
Chemical recycling also opens up the possibility of upcycling: making chemical products from the monomers that are more valuable than plastics, and difficult to produce by other means. “Usually these are not large scale chemicals,” Bardow says, but some still have key roles in certain industries, such as 3-hydroxy-γ-butyrolactone, which is used to produce cholesterol-lowering statin drugs. The high value of these compounds could provide a financial push to develop chemical recycling technology, Bardow says.
A huge barrier to chemical recycling is that plastic polymers are very stable—which is what makes plastics so useful in such a wide variety of applications—so it takes a lot of energy to break them apart. Researchers are looking for enzymes and catalysts that could reduce the energy required. “That’s really where the game is right now for chemical recycling,” Robertson says.
Natural inspiration
To look for the enzymes and catalysts that could aid chemical recycling, “we can go to places where they’re already present in nature”, says Craig Criddle, who specializes in microbial biotechnology at Stanford University in California. (Criddle was a PhD co-adviser to Morse; some of the approaches Mango Materials uses came out of work from his laboratory.) Polymers of various sorts are common in the biological world, and sometimes organisms’ solutions for breaking down natural polymers can be harnessed to disassemble human-created ones, he says. Criddle’s research focuses on mealworms (Tenebrio molitor), which he dubs “tiny little bioreactors”. These invertebrates can digest multiple plastics with the help of their gut microbial community. Other researchers have identified bacteria that can break down multiple types of plastic into the same end product, more evidence that specific microbes—or molecules derived from them—could help with recycling mixed plastic-waste streams.
Researchers are looking to the natural world to make other aspects of the plastics industry more sustainable and circular as well. There has been a surge of interest in plastics produced from renewable feedstocks such as sugar and corn rather than fossil fuels. However, these bioplastics still only account for a small fraction of plastics produced today, and if that were to scale up significantly it could create pressure on agricultural lands and water supplies. These concerns inspired Mango Materials to produce its P3HB from methane, a potent greenhouse gas that is a product of wastewater treatment plants, landfill sites and agricultural facilities. Methane is cheaper than other renewable feedstocks—and plastic is a more valuable material than other products that can be made from methane, Morse explains.
But there are downsides to bioplastics. “They’re typically different polymers” than those made from fossil fuels, Syberg says. “So they don’t fit very well into the recycling systems that we have at the moment.” Take P3HB: the technology exists to recycle it, but the facilities do not, because so little of it is currently produced. (P3HB is also biodegradable in home compost piles, providing another disposal solution.)
Beyond recycling
By 2050, global plastic demand is projected to nearly triple to 1,100 million tonnes per year. In an analysis released earlier this year7, Bardow and his team found that scaling up recycling, relying more on renewable feedstocks and implementing other strategies to make the plastic industry more circular could keep the current level of plastic production within “planetary boundaries”. But if plastic production continues to grow at the predicted pace, then options greatly diminish—and by 2050, Bardow says, there will be no sustainable solution “even with all the tricks that chemists and chemical engineers can pull”.
The findings highlight the need to reduce overall use of plastic, especially single-use items. “If we just turn from making oil-based single-use plastic products to renewable-based single-use plastic products, then we haven’t gotten very far,” says Syberg.
So far, research that could support this transition is scarce. Syberg and his team analysed plastic research relevant to Europe, and found that most studies focus on recycling and the waste phase of plastics, with little attention to other parts of product life cycles8. Similarly, King and Locock conducted a comprehensive review of circular-plastic-economy research worldwide, and found that more than one-quarter of studies focused on recycling, but less than 10% on topics such as repair and reuse9.
Efforts to improve plastic circularity continue. Mango Materials is seeking a location for a facility that could produce up to 2,300 tonnes of P3HB per year—an order of magnitude leap in capability, although still just a tiny fraction of overall global plastics production. “It’s fun to try and be part of the solution,” Morse says. “But it’s also very daunting.”
This article is part of Nature Outlook: Circular Economy, an editorially independent supplement produced with financial support from Google. About this content.
- Zibunas, C., Meys, R., Kätelhön, A. & Bardow, A. Comput. Chem. Eng. 162, 107798 (2022).
- Geyer, R., Jambeck, J. R. & Law, K. L. Sci. Adv. 3, e1700782 (2017).
- Lange, J.-P. ACS Sustainable Chem. Eng. 9, 15722–15738 (2021).
- Tiso, T. et al. Metab. Eng. 71, 77–98 (2022).
- Klotz, M., Haupt, M. & Hellweg, S. Waste Manag. 141, 251–270 (2022).
- Wilson, D. C. & Velis, C. A. Waste Manag. Res. 33, 1049–1051 (2015).
- Bardow, A. et al. Preprint at Research Square https://doi.org/10.21203/rs.3.rs-1788256/v1 (2022).
- Johansen, M. R., Christensen, T. B., Ramos, T. M. & Syberg, K. J. Environ. Manag. 302, 113975 (2022).
- King, S. & Locock, K. E. S. J. Clean. Prod. 364, 132503 (2022)